Extrusionsteile aus Kunststoff – Das sind die Vorteile
Extrusion gehört zu den weit verbreiteten Verfahrenstechniken zur Herstellung von Bauteilen. Ursprünglich in der Kautschukindustrie entwickelt und vorrangig verwendet, werden mittlerweile dank erweiterter Verfahrenstechniken auch Metalle wie Aluminium verarbeitet.
Dabei werden die Grundmaterialien unter Verwendung von Druck aus einer Öffnung herausgepresst. Diese Öffnung ist derartig gestaltet, dass sie dem Ausgangsmaterial ihre endgültige Form gibt. Um das zu gewährleisten, muss die Masse fest sein und nach dem Herauspressen ihre Form behalten. Als Material eignet sich unter anderem Kunststoff.
Die Vorteile des Extrusionsverfahrens liegen dabei vor allem in der Möglichkeit, komplexe Formen zu erstellen. Im Vergleich zu anderen Verfahrenstechniken in der Industrie kann weiches Material verwendet.
Die Länge des Bauteils kann dabei beliebig lang werden und ist nur durch die Eigenschaften des Materials begrenzt. Das Erzeugnis kann anschließend in der benötigten Länge zugeschnitten werden oder in Überlänge zum Ort der Verwendung transportiert werden, um dort in der benötigten Länge verwendet werden.
So werden Extrusionsteile aus Kunststoff hergestellt
Das Kernelement der Herstellung von Extrusionsteilen aus Kunststoff ist der Extruder. Das jeweilige Verfahren orientiert sich stets an dem verwendeten Material und dessen Eigenschaften. Eine erfolgreiche Extrusion ist ein Zusammenspiel aus Druck und Temperatur.
Je nachdem, wie die Parameter gewählt werden, ergeben sich die verschiedenen grundlegenden Verfahren:
- Kaltextrusion: Druck und Temperatur sind niedrig
- Warmextrusion: Höhere Temperatur als bei der Kaltextrusion
- Heißextrusion: Druck und Temperatur sind hoch
Zwei Arten von Extrudern haben sich in der Industrie durchgesetzt. Der Kolbenextruder wird vor allem bei keramischen Materialien verwendet. Die andere, überwiegend eingesetzte Technik, ist der Schneckenextruder. Dieser ist dem Kolbenextruder überlegen und wird vorrangig verwendet. Nur bei Materialien, die mit einem Schneckenextruder nicht zu verwenden sind, wird ein Kolbenextruder verwendet. Ein weiterer Vorteil des Kolbenextruders gegenüber dem Schneckenextruder ist die geringere Rüstzeit, die vor allem bei häufigem Wechsel des Produkts vorteilhaft ist.
Der Schneckenextruder bearbeitet das Granulat, indem es durch eine Schnecke homogenisiert wird. Dies geschieht durch Druck und Erhitzung auf die Zieltemperatur. Das Erzeugnis wird durch die Düse extrahiert und kann nach einer Abkühlung direkt bearbeitet werden, wie etwa in der Länge abgelängt.
Beim Schneckenextruder kann noch grundsätzlich zwischen dem Einschneckenextruder und dem Doppelschneckenextruder unterschieden werden.
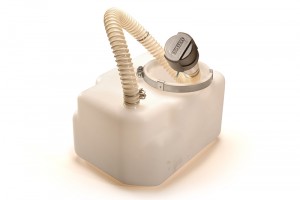
Extrusionsteile aus Kunststoff – Vielfältig im Einsatz
Extrusionsteile aus Kunststoff, Gummi und Metallen begegnen uns im täglichen Gebrauch. Ja, sogar Lebensmittel, wie Nudeln, werden mittels Extrusionsverfahren hergestellt.
Hier einige Beispiele aus dem Alltag.
- Rohre aus Kunststoff
- Schläuche
- Ummantelungen
- Gummis (Scheibenwischer, Dichtungen von Fenster und Tür, Fahrradfelgen)
- Chemiefasern
- Kabelkanäle
Extrusionsteile aus Kunststoff – Das muss ein Anbieter können
Die Herstellung von Extrusionsteilen aus Kunststoff erfordert Wissen über die verschiedenen Verfahrenstechniken und idealen Ausgangsmaterialien. Um den besten Anbieter zu finden, sollten Sie sich bereits früh in der Projektphase mit möglichen Partnern beraten. Je nach Anwendungszweck und Material bestehen unterschiedliche Möglichkeiten der Produktion.
Je genauer Sie die Produktion planen, desto effizienter und somit kostengünstiger kann die Herstellung der Extrusionsteile aus Kunststoff erfolgen.
Unsere langjährige Erfahrung wird Sie dabei unterstützten, bereits in Ihrer Planungsphase die richtigen Weichen zu stellen. Am Ende steht ein durchdachtes und trotzdem kostengünstig produziertes Extrusionsteil aus Kunststoff.
Kontaktieren Sie uns, wir beraten Sie gerne.
Armin Klepsch | CEO
Ich freue mich auf Ihre Anfrage!
Firma: KSE Kunststoff, Spritzguss & Formenbau
Adresse: Rankestraße 32, 90461 Nürnberg
Tel: +49 (0) 911 / 21 65 05 63
E-Mail: info@formenbau-spritzguss.de